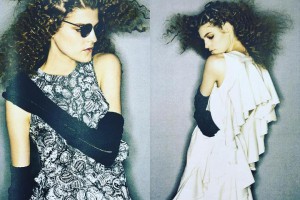
どんな仕事にしたって楽しく思えなかったら長くは続かない
2016-03-23
目次
おはようございます。。今日もまだまだ寒いです
桜が咲きはじめる頃がなんだか好きなファッションいずみのミズイデ@fashionizumiです。
独立して25年経ちました、26度目の春です。
そう、独立したのが1991年の節分でしたから一カ月が過ぎようやく落ち着きはじめて、
よし、これからやったるぜ!って気合十分だったのを思い出します。
さて、今日のブログは。
縫製工場は同じ洋服を何十枚、何百枚、何千枚と縫います。
ボクが修行していた縫製工場の生産方法は、縫製スタッフ(縫直)20名程で先工程、中間工程、組立工程に各自担当が与えられてその日のうちに何十枚と洋服が縫い上がって行きました。
縫い上がった洋服にボタンホールを開ける場合は外注の穴かがり屋さんへ持っていき、その後、内職の方の家へ釦付けとかスナップ付けなどを持っていき、その後、仕上げプレス屋(外注)さんへ持ち込んでそこから納品してもらってた。
その方法は、人数が少ない事業所ても大体同じやり方してました。極端な事例を挙げると、夫婦二人でも同じ。
前工程、中間工程を外注(その当時はミシン内職さんも多かった)に出して組立を親父がと言った図式です。
ボクも独立して同じような方法で仕事してました。
しかし、徐々にそのやり方が時代に合わなくなってきました。
昭和の頃は今に比べて洋服の作り方が雑でもよかった。もちろん、高級婦人服は別です一般婦人服です。
それでもそこそこの値段で売ってましたが、それらの洋服が徐々に日本で作られなくなってきて僕らはプレタポルテと呼ばれる洋服を手掛ける様になったのです。
大きな違いは、9号ワンサイズで100枚以上あったのが7号9号11号13号4サイズ展開で100枚以下になったのとデザインも複雑になりパーツ数が多くなったことですね。そうすると、先ず裁断を裁断屋(外注)に頼めなくなった。
当時加工賃の10%が相場として裁断してもらっていたけれど裁断のパーツが多くなり値上げを求められたが加工賃は変わらずなので、外注には出さなくなった(より正確な裁断が求められたりもしたのもあります)。
縫製も、10人以上の単純作業ライン生産だと手が空く人が出てしまってやり方を変えられない工場は淘汰されていった。
結局は少人数の班(3人4人)で各自が複数工程を担当する多能工の生産システムが生き残り策でした。
できるだけ内製化しようとしました。それは、QR(クイックレスポンス)生産が時代の流れだったから投入から納期まで日にちが無くなってきたのです職出しされたら30日後には納品して欲しいみたいな感じ。
裁断して極力その日に縫い上げるものしか手を付けないようにしました。よくあるポケットの袋ばっかりが全部できてしまっている状態は避けるようにした。
仕掛品を作らない作戦です4人いれば、その間には必ず仕掛が発生しますがそれも最小限にします。
仕掛品は在庫にあたります在庫は売り上げにならないから悪って考え方。
在庫は悪。
仕掛品=納品していない状態=在庫=悪。
ってことは、縫い上がって、ボタンホール開けて、仕上げプレスまでして納品できる状態にして完成なわけです。
それをするには全て内製化ですそうしないと無理です正直言うと、まとめ(釦付け等)は内職さんにお願いしてます。
でも、ボタンホール指示もなくまとめ箇所もないアイテムならその日のうちに仕上げプレスまでして出荷できる体制を確立しました。これぞ理想の生産システムだと思います。
まあ、当社は人数が少なくて1日に上がっても20着程度だから無理なくできましたが、これが30人規模の松ノ木縫製産地を見た時には「マジですか?!」状態でした。
30人規模だと1日に100着前後は上がってきます(協力工場分もありますし)。
しかし、仕上げプレス担当者は社長ともう一人の二人だけなんです(実質1人です)。
うちと同じでまとめは内職さんで中一日後上がってきたら仕上げして出荷のローテーション内職さんの家にはハンガーに吊るして移動します(皺にならない様に)。
そう、縫製現場で縫い上がったらもうほぼ完ぺきな状態に仕上がっているのです仕上げプレスは軽くシワを伸ばして終わり。
じゃないとそれだけの枚数を1人でこなすのは無理っす、言わば縫製現場で既に完成されている生産システムです。
全ての縫製スタッフが縫っている洋服の完成形を理解しているから問題解決も早いし不良品発生率ゼロ、在庫ゼロ、指示ゼロ
夢のような生産システムです。高品質な洋服を作るには縫う人が洋服の事を理解していることが必須です。
ただわけもわからず作業しているだけの人はいないのです。
管理された生産システムの場合、工場長クラスの人が縫い上がった製品を検品したり指導したりしているそんな印象があります。その方法だと、ミスに気付くのが遅くなると思います気が付いたら不良在庫の山。おそろしい・・・
直すと3倍の時間が掛かります縫った時間が無駄になり、解く時間が掛かり、更にまた縫い直すわけですから。
ミスに早く気付く為には、現場の縫製スタッフの理解力を上げるのが近道だと言えます。
そんな方法を惜しみなく教えてくれる人が近くにいて良かった本当に感謝です。
在庫ゼロ生産システムはボクの中では松ノ木生産システムと呼んでいます。松ノ木生産システムのいいところは早く人が育ちます。だから取り入れてます。
在庫ゼロを意識して工程を分けるとどんな小ロットでも対応できるようになりました。ただ、裁断は間に合わなくなりますが気合でガンバリマス。
丸縫いデキる縫製職人をより速く育成できれば、サンプルシーズンも楽勝に乗り切れる様になります。(なるはずです)
そうなれば、今できなくてお断りしている依頼にもお応えできるようになりますのでお客様にも喜ばれると思う。そんな日が来るのも遠くないような気がしてる。
ファッションいずみの今後に乞うご期待っす!がんばります。
洋服で困ったことがあったらお気軽にお問合せください。
お友だち追加してね、直接ミズイデにメッセージが送れますよ。
お直しをどこに頼んだらいいのか悩んだり、お店を探して持って行ったりする時間がもったいないと感じたら、おおよその料金を確認することがスマホひとつでできます。
洋服のお直しでお困りならファッションいずみ公式LINEアカウントが簡単で便利です。LINEをご利用であれば下の友だち追加ボタンをクリックするだけ。
LINEを使って直したい洋服の写真を全体・部分・更に寄りで3枚送ってください。リメイクの場合はイメージ画を描いてもらえるとお見積りを出しやすいです。
洋服を送るのに畳んで小さくなる洋服ならレターパックが便利です。コンビニから宅配便で送ってね。
洋服お直しが完了(お預かりして1週間くらい)したらレターパックか佐川急便で送ります。お支払いは square というオンラインチェックアウトでクレジットカード決済が便利です。お振込みでも大丈夫(LINEでお伝えください)。
お直しに関することならなんでもお気軽に相談してください。
メールでのお問合せは公式サイトから。メールフォームが開きます。
https://www.fashion-izumi.net/contact/
お電話でのお問合せは平日10時から18時までとさせていただいてます。
〒338-0812 埼玉県さいたま市桜区神田154-4-2F
営業時間 平日9:00~18:00 土曜日要予約・日曜祝祭日定休